All of my CNC work up to this point has been two dimensional. I draw lines and then have the machine cut them to a certain depth. But there’s a whole other world of three dimensional carving that I have never tried so I invented a project to learn a bit about that.
For a model, I picked a Luther Rose model from Thingiverse. I brought it into Fusion 360 and spent a long time learning about all the different 3D tool paths that it has. I knew that I wanted to do one roughing pass to get rid of most of the material and then do a finishing pass with a much smaller bit to get the detail. I planned the first pass with a 1/8″ endmill and then a follow up with a 1/16″ ball nose mill. (I had to buy a special collect to hold the 1/16″ endmill because it only had a 1/8″ shank.)
From there it was off to the CNC to try it out. What followed was a long series of errors. The board would slip, I’d lose my zero when I changed bits and not be able to reset it, the bit would slip in the chuck etc. I started with some cheap pine boards and eventually moved to 3″ walnut squares.
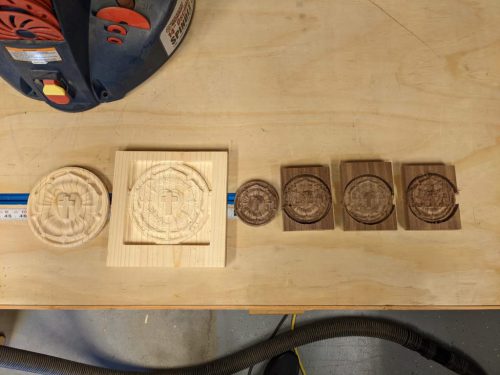
With much perseverance, I finally got it dialed in! On the 3″ walnut pieces, the first pass took about an hour and then the second pass would take 3-4 hours. Usually I stay in the garage when the CNC is running, but this was the first time that I let it run attended. I would go out and check on it regularly and I’d watch it via the camera in the garage. Working from home was a big advantage because I could run it throughout the day while I worked.
After I made four successful roses and ran out of the walnut board, I felt like I still had more to learn. I also had some very wide scraps of wood leftover from the dresser build. So next I set out to make a couple 8″ roses out of cherry. I switched to a 1/4″ endmill for the first pass and an 1/8″ ball mill for the finishing pass to keep the total time down. Neither one of those cherry roses was flawless, but with a lot of sanding afterwards, they look great. And then the pièce de résistance was a 9.5″ wide piece of walnut. That one started warping a bit as I cut it, but I was able to salvage it with a lot of hand sanding.
It was a huge learning experience, but it was also a lot of fun. I feel like I’ve unlocked a new woodworking skill! There’s still plenty to learn, but I won’t avoid a project if I need to do some 3D stuff on the CNC.
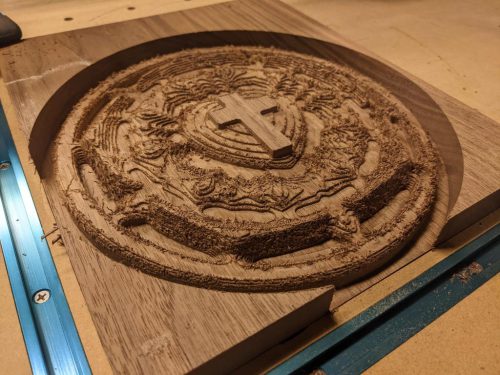
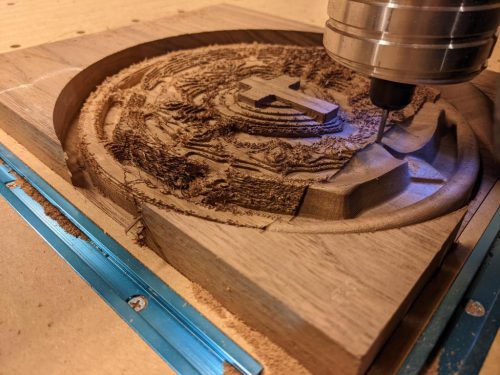
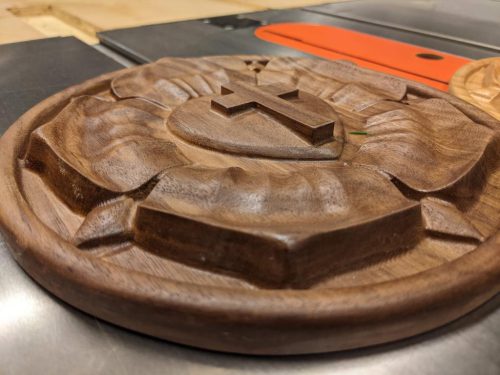
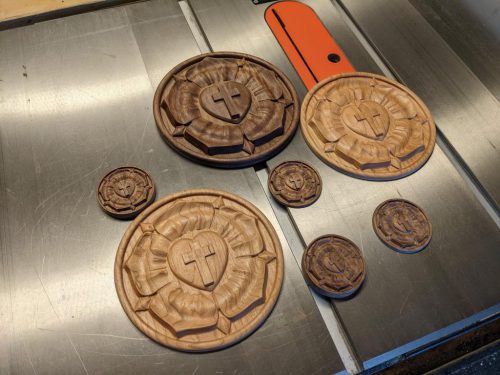
Follow me on Instagram @martenswoodworks. I usually post mid-project updates to stories and then make posts for the finished projects.